快走丝线切割在加工过程中往往会出现断丝现象,致使加工停顿,不得不从头开始,浪费了大量时间,破坏了加工表面的完整性,增加了加工的困难。下面从实际生产的角度出发,就断丝的问题进行分析,并提供解决办法。 一、与电极丝相关的断丝 1.电极丝的选择 电极丝的选择不外呼是电极丝的种类及直经。一般来说,在测量丝径比新丝减少0.03~0.05mm时,应时更换新丝。一般常选择0.18mm钼丝为快走丝的电极丝,则不易断丝。 2.丝张力及走丝速度 电极丝在切割过程中,其张力大小要适当。由于储丝筒上的电极丝在正反运动时的张力不一样,工作一段时间后电极丝会伸长 ,致使张力下降,张力下降的后果是抖丝加剧,极易断丝。值得注意的是,电极丝的张力也不能提高得太大,否则电极丝内应力增 大,反而也会断丝。 二、与工件相关的断丝 1.未经锻打、淬火、回火处理的材料,钢材中所含碳化物颗粒大,聚集成团,且分布又不均匀,存在较大的内应力。如果工件的内应力没有得到消除,在切割时,有的工件会开裂,把电极丝碰断,有的会使间隙变形,切缝变窄而卡断电极丝。 切割较厚的铝材料时,导电块磨损较大,会使电极丝的摩擦力过大,易将电极丝拉断,应注意及时更换导电块. 2.加工薄工件时的断丝 薄工件一般指其厚度在3mm以下。解决的办法是减少脉冲放电能量;也可在上下导轮之间采用辅料加厚的方法,加大厚度以增加阻尼,也可防止钼丝抖动,这种方法较简便,而且不需调整加工电参数。 3.加工厚工件时的断丝厚工件一般指大于100mm的工件。在加工快要结束时,可用磁铁吸住将要下落的工件,或和者人工保护下落的工件,使其平行缓慢下落从而防止砸断电极丝。 4.工件在平磨以后应退磁。若工件未退磁,电火花线切割加工中产生的电腐蚀颗粒易吸附在割缝中,特别是工件较厚时,不退 磁易造成切割进给不均匀,造成短路、断丝。 三、与电参数选择相关的断丝 电火花线切割的电参数包括电压、电流、脉冲宽度、脉冲间隙、功放管等。在加工时如果电参数选择不当是会引起断丝。 四、与走丝装置及工作液相关的断丝 1.与走丝装置相关的断丝 机床运行到一定时间其走丝装置精度变差,尤其是导轮的磨损,会增加钼丝的抖动,破坏火花放电的正常间隙,易造成大电流 集中放电,从而增加断丝的机会。 2.与工作液相关的断丝 工作液在使用较长时间后,变得脏污、综合性能变差是引起断丝的重要原因。根据加工经验,新工作液每天工作8h,使用两天 后效果最好,继续使用8~10天则易断丝,需要更新的工作液。 长沙金奥新材研发生产的环保型线切割工作液,可以使用三至六个月不换水而不会加剧断丝的机率,其本身就有钼丝损耗小、无泡易洗的优点,深受广大用户的喜爱。
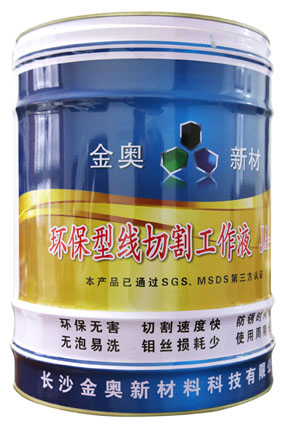 |